Industrial Magnetic Tools Revolutionizing Modern Manufacturing
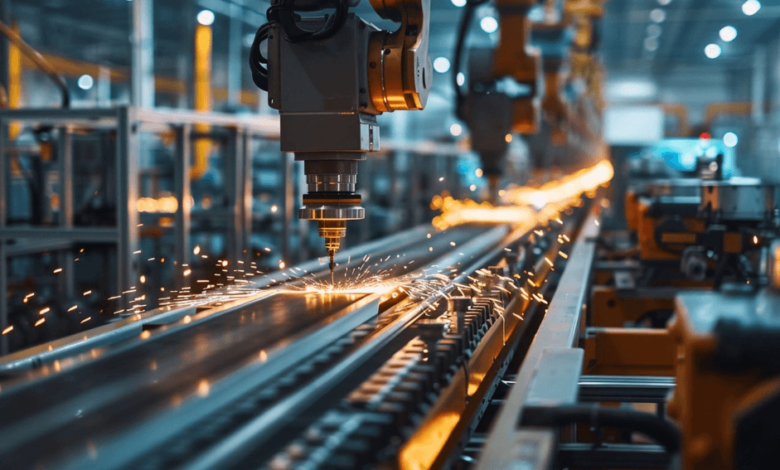
The manufacturing industry constantly evolves, driven by technological advances and the need for efficiency. One of the most impactful innovations is the use of industrial magnetic tools. These tools have transformed how raw materials are handled, produced, and assembled. Whether lifting heavy loads, separating materials, or aligning components with precision, magnetic tools have proven indispensable in modern factories, workshops, and production lines.
The Role of Magnetic Tools in Manufacturing
Industrial magnetic tools harness the power of magnetism for a wide range of manufacturing applications. They solve critical challenges, including operational efficiency, worker safety, and product quality. Their versatility has made them staples in industries like automotive, aerospace, construction, and electronics.
Enhancing Efficiency
Magnetic tools excel at speeding up manufacturing processes. For instance, magnetic lifters allow workers to move heavy materials, such as steel plates and iron components, without manual handling or additional equipment like clamps or hooks. This not only reduces the time spent on transport but also minimizes labor costs.
Magnetic chucks and fixtures are also widely used in machining operations. By securely holding metal parts in place, they ensure stability and reduce vibrations during cutting, grinding, and drilling processes. This leads to higher precision and faster machining.
Improving Workplace Safety
Workplace safety is a top priority in any manufacturing facility. Magnetic tools contribute significantly by minimizing the need for manual handling of heavy or hazardous materials. Magnetic separation systems, for example, can remove metallic contaminants from bulk materials, preventing damage to machinery and reducing workplace hazards.
Electromagnetic tools, paired with advanced control systems like the rectifier controller, ensure consistent and reliable operation while lowering the risks of abrupt power loss. This guarantees worker safety and reduces the likelihood of equipment damage.
Types of Industrial Magnetic Tools
Over the years, various magnetic tools have emerged, each designed to address specific manufacturing needs. Below are some of the most commonly used tools and their applications:
Magnetic Lifters
Magnetic lifters are designed to move large and heavy metallic objects. They use permanent or electromagnets to grip materials securely and are invaluable in industries handling steel plates, pipes, and other heavy components. Unlike mechanical gripping systems, magnetic lifters don’t damage surfaces, making them ideal for sensitive materials.
Magnetic Separators
Magnetic separators are used to sort and purify materials effectively. They remove ferrous particles from powders, liquids, and bulk solids. These separators are integral to industries such as food processing, mining, and recycling, where contamination control is critical.
Magnetic Chucks
Magnetic chucks provide firm and stable clamping for machining or grinding tasks. By eliminating the need for mechanical clamps, they allow for unobstructed cutting and superior finish quality. They are often used in CNC machines and lathes for precise work.
Magnetic Sweeper Tools
Magnetic sweepers help maintain clean and safe workspaces. They pick up metallic debris such as nails, screws, or shavings, reducing workplace hazards and maintaining machine integrity.
Benefits of Magnetic Tools in Manufacturing
The adoption of industrial magnetic tools brings a range of benefits that go beyond traditional methods.
Increased Productivity
Magnetic tools simplify complex tasks, making processes faster and less labor-intensive. This directly impacts production output and allows manufacturers to meet rising demand efficiently.
Reduced Maintenance Costs
Magnetic systems are known for their durability and reliability. They have fewer moving parts compared to mechanical systems, reducing wear and tear and lowering maintenance costs. Additionally, magnetic separators prevent damage to machinery by removing harmful metallic impurities.
Higher Precision and Consistency
Magnetic tools ensure repeatability and precision in tasks like machining or material handling. Their ability to maintain stability ensures consistent quality in finished products, building trust with customers and stakeholders.
See also Why Port & Company Is a Go-To Brand for Custom Clothing
The Future of Magnetic Tools in Manufacturing
The future of industrial magnetic tools looks promising as technological advancements continue to enhance their capabilities. Smart magnets integrated with IoT (Internet of Things) devices are set to revolutionize how tools are monitored and controlled. Operators can adjust settings remotely, monitor tool performance in real-time, and predict maintenance needs well in advance.
Additionally, developing stronger and more compact magnetic materials, such as neodymium-based magnets, will pave the way for lighter yet more powerful tools. This can significantly expand their use cases across sectors, including renewable energy and microelectronics.
Integrating renewable energy sources into electromagnetic systems may reduce energy consumption, making them more sustainable. Magnetic tools are poised not only to optimize manufacturing processes but also to support greener operations in the industrial sector.
Industrial magnetic tools have become an essential backbone of modern manufacturing. Their ability to enhance efficiency, precision, and safety makes them a worthwhile investment for industries. While the innovation in this field has been remarkable, the possibilities for future developments remain vast. By harnessing magnetic technology, manufacturers can remain agile, competitive, and prepared for the challenges of tomorrow’s market.