Selecting Pigging System Solutions: A Practical Guide for Efficiency-Focused Manufacturers
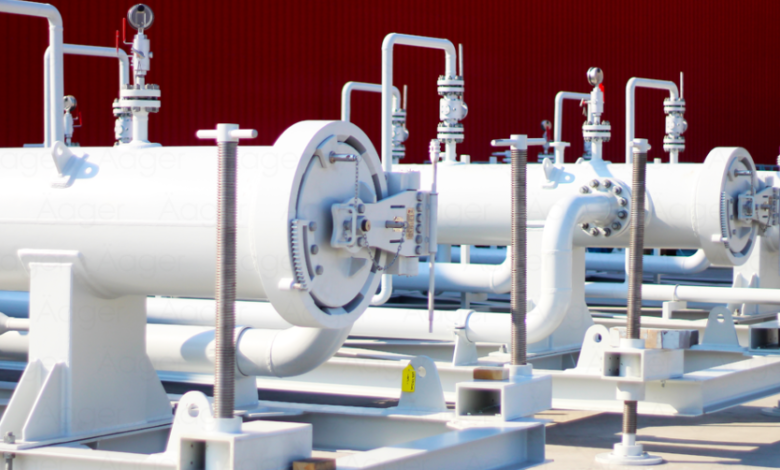
Modern manufacturing is driven by efficiency, sustainability, and cost-effectiveness. In industries where fluids or viscous products flow through pipelines—such as food, beverage, chemicals, cosmetics, and pharmaceuticals—one powerful tool has emerged to maximize yield and streamline operations: pigging. However, the true challenge lies not in recognizing the benefits of pigging, but in selecting pigging system solutions that are perfectly matched to a facility’s unique needs.
Pigging systems are designed to recover residual product from pipelines, reduce cleaning time, and eliminate waste. But the benefits are only as good as the system’s design and compatibility. This article explores a clear roadmap for selecting pigging system setups tailored to real-world production requirements.
Understanding Pigging Systems in Practice
At its core, a pigging system uses a device (called a “pig”) that is inserted into a pipeline and pushed along with product or pressure to recover any leftover material. This process is common in batch production lines and is invaluable for product changeovers, cleaning, and minimizing waste.
Depending on the setup, a pigging system may be manual, semi-automated, or fully automated. Modern designs integrate seamlessly into production lines and can be adapted for CIP (Clean-In-Place) or SIP (Sterilization-In-Place) operations.
When selecting pigging system solutions, understanding the full process flow, product characteristics, and pipeline conditions is critical.
Step 1: Define Your Goals and Challenges
The starting point for selecting pigging system equipment is clearly outlining what you want the system to achieve. This may include:
- Recovering high-value or high-volume product from pipelines
- Reducing water or chemical usage in cleaning processes
- Minimizing changeover downtime between product runs
- Increasing pipeline hygiene or preventing cross-contamination
- Complying with environmental or food safety regulations
Once goals are identified, outline the biggest challenges your current system faces. These could include frequent contamination, product loss, long cleaning cycles, or labor inefficiencies.
See also: custom smartphone manufacturer: The Strategic Tech Partner for Business Innovation
Step 2: Know Your Product Characteristics
Product type is one of the most influential factors when selecting pigging system components.
Ask the following questions:
- Is the product viscous (like creams or pastes) or free-flowing (like beverages or syrups)?
- Does the product leave residue that is hard to clean?
- Is the product reactive with certain materials (e.g., acidic, alkaline, or solvent-based)?
- Are multiple types of products processed through the same pipeline?
These factors affect the type of pig required, material compatibility, sealing efficiency, and system design.
Step 3: Assess Your Pipeline Layout
Pigging system success is directly tied to how well it integrates with your existing pipeline setup. Consider:
- Pipeline diameter and length: Determines the size and type of pig needed
- Bends, elbows, and vertical sections: Affects pig movement and required propulsion
- Access points for pig launchers and receivers: Must be accessible and secure
- Multiple product lines: May require switching valves or a multi-line pigging setup
A qualified pigging system provider should inspect or model your pipeline layout before recommending a solution.
Step 4: Decide on Automation Level
Automation level significantly influences cost, efficiency, and usability. When selecting pigging system features, consider your facility’s manpower, batch size, and production frequency.
- Manual systems: Suitable for low-volume applications. Require operators to insert and remove pigs, and manually start cleaning processes.
- Semi-automated systems: Include controls or sensors for some steps but still require operator involvement. Ideal for mid-sized operations.
- Fully automated systems: Integrated into PLCs or control systems. Offer consistent, hands-free operation with higher precision and safety. Best for large-scale production.
Automation also improves traceability and data logging for audits and regulatory purposes.
Step 5: Choose the Right Pig for Your System
The pig is the heart of any system. When selecting pigging system components, the pig must match your process environment and product type.
Types of pigs:
- Solid pigs: Durable, ideal for long straight pipelines
- Foam pigs: Lightweight and flexible, good for tight bends
- Sanitary pigs: Designed for hygienic industries with FDA-compliant materials
- Intelligent or “smart” pigs: Equipped with sensors for diagnostics (mostly used in oil and gas)
Consider how the pig will be cleaned, stored, and tracked. Also assess wear rate, compatibility with pipeline materials, and risk of product contamination.
Step 6: Review Cleaning and Maintenance Requirements
Pigging systems reduce cleaning needs but must also be easy to maintain themselves. A good system should include:
- Quick access to pigs and key components
- Replaceable parts for seals, launchers, or valves
- Clear indicators or detection sensors for pig position
- Documentation for safe handling and servicing
In food, cosmetic, or pharma settings, hygienic design should meet EHEDG or 3-A Sanitary Standards. For chemical use, resistance to corrosion or solvent breakdown is essential.
Step 7: Analyze Return on Investment (ROI)
When selecting pigging system solutions, ROI can be measured in several ways:
- Product recovered per batch/year: e.g., reclaiming 20 liters per run × 500 runs/year = 10,000 liters saved
- Reduced labor and cleaning time: Faster changeovers free up staff and increase capacity
- Savings on water, chemicals, and energy: Environmental and cost savings
- Reduced downtime: More uptime means more output and revenue
Most manufacturers recoup their investment in under 18 months—often faster for high-volume or high-value products.
Step 8: Work with a Trusted Partner
Not all suppliers provide the same level of quality or customization. When selecting pigging system vendors, choose partners that:
- Understand your industry (e.g., food vs. industrial chemicals)
- Offer customized design and installation
- Provide commissioning, training, and technical support
- Can supply spare parts and long-term maintenance plans
Avoid off-the-shelf systems unless your operation is highly standardized. A one-time investment in customization pays dividends long-term.
Conclusion
selecting pigging system components and designs is a strategic decision that involves far more than just ordering a pig and launcher. It requires a careful study of your product types, pipeline configurations, operational goals, regulatory demands, and future scalability.
When done right, a pigging system will significantly improve your bottom line, reduce environmental impact, and enhance product integrity. It also plays a key role in maintaining pipeline integrity by preventing buildup, reducing corrosion risk, and supporting early detection of potential issues. Whether you’re handling food-grade ingredients, harsh chemicals, or multi-product pipelines, a well-designed pigging solution becomes an integral part of smart, sustainable production.