How to Choose the Right Rubber Dock Bumper for Your Truck Dock (With Size Guide)
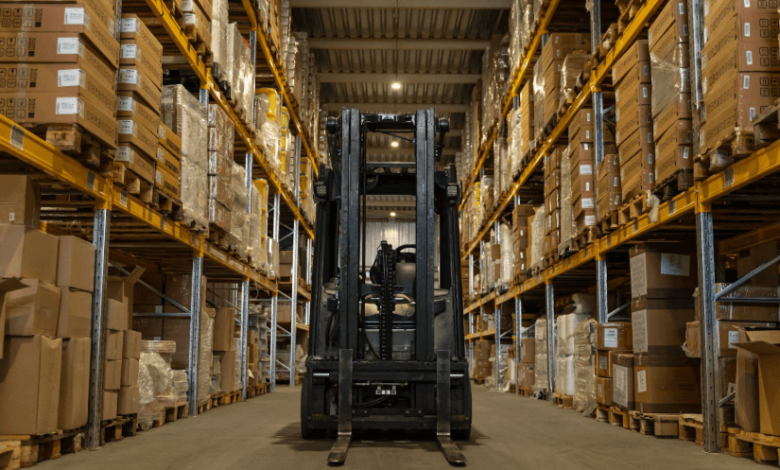
Introduction to Rubber Dock Bumpers
Rubber dock bumpers for trucks serve as the crucial protective barrier between your loading dock and incoming trucks, preventing costly damage to both your facility and visiting vehicles. These essential components absorb the impact when trucks back up to your dock, creating a safe and secure connection point for loading and unloading operations. The selection of the right rubber dock bumper is not merely a matter of choosing any available option, but rather a strategic decision that impacts operational efficiency, safety, and long-term cost management.
The loading dock environment presents unique challenges that require careful consideration of multiple factors. Trucks of varying sizes, weights, and approach angles regularly interact with your dock throughout the day. Without proper protection, these interactions can result in significant structural damage, equipment malfunction, and potential safety hazards for workers. The right rubber dock bumper system acts as the first line of defense, absorbing kinetic energy and distributing impact forces across a wider surface area.
Modern rubber dock bumpers have evolved significantly from their basic predecessors. Today’s options incorporate advanced materials, innovative designs, and enhanced durability features that provide superior protection while maintaining cost-effectiveness. Understanding the various types, specifications, and installation requirements will help you make an informed decision that serves your facility’s needs for years to come.
Understanding the Importance of Proper Dock Bumper Selection
The significance of selecting appropriate rubber dock bumpers extends far beyond simple impact absorption. Your choice directly influences operational efficiency, worker safety, equipment longevity, and overall facility maintenance costs. When trucks repeatedly impact inadequate or improperly sized bumpers, the resulting damage can cascade throughout your entire loading dock system.
Proper dock bumper selection begins with understanding the specific demands of your facility. High-traffic loading docks that service multiple truck types throughout the day require different protection than facilities with occasional, predictable deliveries. The frequency of use, variety of truck sizes, and approach angles all contribute to the stress placed on your bumper system.
The economic implications of poor bumper selection become apparent over time. Inadequate protection leads to structural damage, requiring expensive repairs to dock walls, levelers, and surrounding infrastructure. Additionally, damaged bumpers must be replaced more frequently, creating ongoing maintenance costs and potential operational disruptions. The initial investment in quality rubber dock bumpers pays dividends through reduced maintenance expenses and extended equipment life.
Safety considerations cannot be overlooked when evaluating dock bumper options. Properly functioning bumpers contribute to a safer working environment by providing predictable truck positioning, reducing sudden impacts, and maintaining consistent spacing between vehicles and dock equipment. Workers can operate with greater confidence when they know the protection system is reliable and appropriate for the traffic patterns they encounter daily.
See also: Business Productivity Tools: How Audio-to-Text Conversion Boosts Workplace Efficiency
Types of Rubber Dock Bumpers
Understanding the various types of rubber dock bumpers available helps narrow your selection to options that best match your facility’s specific requirements. Each type offers distinct advantages and limitations that should be evaluated against your operational needs and budget constraints.
Laminated rubber dock bumpers represent the most common and versatile option for many facilities. These bumpers consist of multiple layers of rubber bonded together, creating a dense, durable barrier that effectively absorbs impact while maintaining structural integrity. The laminated construction allows for consistent performance across a wide range of impact forces and provides excellent resistance to weathering, chemicals, and UV exposure. These bumpers typically offer the best balance of performance, durability, and cost-effectiveness for general-purpose applications.
Molded rubber dock bumpers provide enhanced performance characteristics through their specialized manufacturing process. Created using compression molding techniques, these bumpers offer superior density consistency and can be engineered with specific hardness ratings to match your facility’s requirements. The molding process allows for more precise dimensional control and can accommodate custom shapes or mounting configurations. While typically more expensive than laminated options, molded bumpers often provide longer service life and better performance in demanding applications.
Steel-faced rubber dock bumpers combine the impact absorption properties of rubber with the durability and wear resistance of steel plating. These hybrid systems excel in high-traffic environments where standard rubber bumpers might wear prematurely. The steel facing protects the rubber core from abrasion and impact damage while maintaining the energy-absorbing characteristics essential for effective operation. These bumpers require careful consideration of mounting systems and may need specialized installation procedures.
Specialty rubber formulations address specific environmental challenges that standard bumpers cannot handle effectively. Cold-weather formulations maintain flexibility and impact absorption in sub-freezing temperatures, while chemical-resistant compounds protect against exposure to corrosive substances. These specialized options command premium prices but provide essential protection in challenging environments where standard bumpers would fail prematurely.
Key Factors to Consider When Choosing Dock Bumpers
Selecting the appropriate rubber dock bumper requires careful evaluation of multiple factors that influence both immediate performance and long-term effectiveness. Understanding these considerations ensures your investment provides optimal protection and value throughout its service life.
Traffic volume and frequency significantly impact bumper selection requirements. Facilities with constant truck traffic throughout multiple shifts require more robust protection than those with occasional deliveries. High-frequency operations generate more accumulated stress on bumper systems, necessitating higher-grade materials and more frequent inspection schedules. Consider both current traffic patterns and anticipated future growth when evaluating capacity requirements.
Truck size and weight variations present another crucial consideration. Loading docks that accommodate everything from small delivery vans to large tractor-trailers need bumpers capable of handling the full range of impact forces. Heavy vehicles generate significantly more kinetic energy during docking procedures, requiring bumpers with greater compression resistance and energy absorption capacity. Document the typical vehicle types servicing your facility to ensure adequate protection for all scenarios.
Environmental conditions play a vital role in bumper material selection and longevity. Facilities located in regions with extreme temperature fluctuations need bumpers formulated to maintain performance characteristics across the full temperature range. Exposure to chemicals, oils, or other potentially damaging substances requires specialized rubber compounds that resist degradation. UV exposure from sunlight can cause premature aging in standard rubber formulations, making UV-resistant options essential for outdoor installations.
Dock configuration and approach angles influence both bumper type and mounting requirements. Straight-in approaches allow for standard rectangular bumpers, while angled approaches may require specialized shapes or additional protection. The height relationship between typical truck bed levels and your dock platform affects bumper positioning and may require adjustable mounting systems. Consider the full range of vehicles and approach patterns when evaluating configuration options.
Size Guide and Measurements
Proper sizing of rubber dock bumpers requires precise measurements and careful consideration of the relationship between truck characteristics and dock configuration. Incorrect sizing can result in inadequate protection, premature wear, or operational difficulties that compromise safety and efficiency.
Standard dock bumper dimensions typically range from 4 inches to 24 inches in width, with heights varying from 10 inches to 36 inches. Thickness measurements commonly fall between 3 inches and 8 inches, depending on the level of protection required. These dimensions must be matched to both the dock configuration and the typical vehicles servicing your facility to ensure optimal performance.
Width measurements should account for the full range of truck body styles and approach angles encountered at your facility. Narrow bumpers may provide adequate protection for consistent, straight-in approaches but can be bypassed by vehicles with slight angular approaches. Wider bumpers offer greater coverage but may interfere with door operations or create clearance issues in tight spaces. Consider the trade-offs between coverage and operational convenience when selecting width specifications.
Height considerations involve matching bumper dimensions to typical truck bed levels and dock platform heights. The bumper should extend sufficiently above and below the expected impact zone to accommodate variations in vehicle suspension, loading conditions, and approach angles. Inadequate height coverage can result in impacts above or below the protected area, causing damage to unprotected surfaces.
Thickness requirements depend on the kinetic energy levels generated by your typical truck traffic. Heavy vehicles approaching at normal speeds generate significant impact forces that require thicker bumpers with greater compression capacity. Lighter vehicles or controlled-speed environments may function adequately with thinner bumpers, providing cost savings without compromising protection. Calculate the typical impact energies for your facility to determine appropriate thickness specifications.
Mounting considerations affect both bumper sizing and installation requirements. Surface-mounted bumpers require adequate wall space and structural support, while recessed installations may allow for larger bumpers without protruding into the dock area. The mounting system must provide secure attachment capable of withstanding repeated impact forces without loosening or failure.
Installation Considerations
Proper installation of rubber dock bumpers is crucial for achieving optimal performance and longevity. Even the highest-quality bumpers will fail prematurely if not installed correctly, making careful attention to installation procedures essential for protecting your investment.
Wall preparation forms the foundation of successful bumper installation. The mounting surface must be structurally sound, level, and capable of supporting the forces generated during impact events. Concrete walls may require reinforcement or repair to provide adequate support, while metal surfaces need proper preparation to ensure secure fastener attachment. Any existing damage or structural deficiencies should be addressed before proceeding with installation.
Mounting hardware selection significantly impacts installation success and long-term performance. Fasteners must be appropriately sized and rated for the expected loads, with consideration given to both static weight and dynamic impact forces. Stainless steel or galvanized hardware provides corrosion resistance essential for long-term reliability. The quantity and spacing of fasteners should follow manufacturer recommendations to ensure proper load distribution.
Positioning accuracy affects both protection effectiveness and operational convenience. Bumpers must be located at the correct height to intercept truck impacts while avoiding interference with loading equipment or door operations. Horizontal positioning should center the bumper on the expected impact zone while providing adequate coverage for approach variations. Use precise measurement tools and techniques to ensure accurate placement.
Alignment considerations become particularly important when installing multiple bumpers or replacing individual units within an existing system. Misaligned bumpers can create impact concentration points that accelerate wear and reduce protection effectiveness. Consistent alignment also contributes to a professional appearance and easier maintenance procedures.
Weather protection may be necessary depending on your facility’s location and exposure conditions. Outdoor installations require consideration of water drainage, UV exposure, and temperature cycling effects on both bumpers and mounting hardware. Proper sealing and weatherproofing measures extend service life and maintain appearance over time.
Maintenance and Longevity
Establishing a comprehensive maintenance program for your rubber dock bumpers ensures optimal performance throughout their service life while maximizing your investment return. Regular inspection and maintenance procedures can identify potential issues before they result in costly failures or safety hazards.
Visual inspection procedures should be performed regularly to assess bumper condition and identify signs of wear, damage, or degradation. Look for cracks, tears, or separation in the rubber material that could compromise impact absorption capabilities. Check for signs of compression set, where the rubber fails to return to its original shape after impact, indicating material fatigue. Examine mounting hardware for looseness, corrosion, or damage that could affect installation integrity.
Cleaning procedures help maintain bumper appearance and performance while extending service life. Remove accumulated dirt, debris, and contaminants that can accelerate wear or cause premature aging. Use appropriate cleaning agents that won’t damage rubber compounds or mounting hardware. Avoid harsh chemicals or abrasive cleaning methods that could compromise material integrity.
Damage assessment requires understanding the difference between normal wear and conditions requiring replacement. Surface scuffs and minor abrasions are normal in regular service, while deep cuts, chunks missing from the bumper face, or significant compression set indicate the need for replacement. Document damage progression to establish replacement schedules and identify patterns that might indicate underlying issues.
Replacement timing depends on usage patterns, environmental conditions, and performance requirements. High-traffic facilities may require more frequent replacement than low-usage applications. Environmental factors such as extreme temperatures, chemical exposure, or UV radiation can accelerate aging and necessitate earlier replacement. Establish replacement criteria based on measurable conditions rather than arbitrary time intervals.
Preventive measures can significantly extend bumper service life and reduce maintenance requirements. Proper truck driver training reduces excessive impact forces and improper approach angles that accelerate wear. Installing warning systems or guidance aids helps drivers position vehicles correctly, reducing stress on bumper systems. Regular facility maintenance ensures dock areas remain clear of debris that could interfere with normal operation.
Cost Analysis and Budget Planning
Understanding the total cost of ownership for rubber dock bumpers involves considerations beyond initial purchase price. A comprehensive cost analysis includes installation expenses, maintenance requirements, replacement frequency, and the potential costs of inadequate protection.
Initial purchase costs vary significantly based on bumper type, size, and quality specifications. Basic laminated rubber bumpers typically represent the lowest initial investment, while specialty formulations or steel-faced options command premium prices. However, the relationship between initial cost and long-term value may favor higher-priced options that provide extended service life or superior performance characteristics.
Installation expenses include both material costs and labor requirements. Professional installation ensures proper mounting and alignment but adds to project costs. The complexity of your specific installation affects labor requirements, with straightforward surface mounting typically requiring less time than custom configurations or structural modifications. Consider whether your maintenance staff can handle installation or if professional services are necessary.
Maintenance costs accumulate over the bumper’s service life and should be factored into total ownership calculations. Regular inspection and cleaning require minimal investment but contribute to extended service life. Replacement of mounting hardware, repair of minor damage, and periodic adjustments add to ongoing costs. Facilities with higher traffic volumes or challenging environmental conditions typically experience higher maintenance expenses.
Replacement frequency directly impacts long-term costs and should be estimated based on your facility’s specific conditions. High-quality bumpers in moderate-use applications may provide service for many years, while heavy-duty operations or challenging environments may require more frequent replacement. Document actual service life to refine future replacement planning and budget allocation.
Hidden costs of inadequate protection can far exceed bumper system investments. Structural damage to dock walls, loading equipment, or building components requires expensive repairs and potential operational disruptions. Vehicle damage claims, insurance premium increases, and liability issues represent additional financial risks. Worker injuries resulting from inadequate protection systems can generate significant costs and regulatory compliance issues.
Common Mistakes to Avoid
Understanding common mistakes in rubber dock bumper selection and installation helps avoid costly errors that compromise performance and safety. Learning from these typical oversights ensures your investment provides optimal protection and value.
Undersizing bumpers to reduce initial costs frequently results in inadequate protection and premature failure. Bumpers that are too small for the application cannot effectively absorb impact forces or provide adequate coverage for vehicle variations. The resulting damage to dock structures and equipment quickly exceeds any savings from choosing smaller bumpers. Always size bumpers appropriately for your worst-case scenarios rather than average conditions.
Ignoring environmental factors during selection can lead to premature failure and disappointing performance. Standard rubber compounds may not provide adequate service life in extreme temperature conditions, chemical exposure, or high UV environments. Failing to specify appropriate materials for your specific conditions results in accelerated aging, cracking, or degradation that necessitates early replacement.
Improper installation techniques compromise even high-quality bumpers and create safety hazards. Inadequate mounting hardware, poor surface preparation, or incorrect positioning reduces protection effectiveness and may result in bumper failure during impact events. Following manufacturer installation guidelines and using appropriate tools and techniques ensures optimal performance and longevity.
Neglecting maintenance requirements allows minor issues to develop into major problems that require expensive repairs or replacement. Regular inspection and cleaning procedures are essential for identifying wear patterns, damage, or mounting issues before they compromise performance. Establishing maintenance schedules and procedures prevents costly failures and extends service life.
Choosing bumpers based solely on price without considering performance requirements often results in false economy. Low-cost options may provide adequate short-term protection but fail to deliver acceptable long-term value. Consider total cost of ownership, including installation, maintenance, and replacement costs, when evaluating options.
Safety Regulations and Compliance
Compliance with safety regulations and industry standards ensures your rubber dock bumper installation meets legal requirements while providing adequate protection for workers and equipment. Understanding applicable regulations helps avoid costly violations and potential liability issues.
OSHA requirements address various aspects of loading dock safety, including provisions for adequate truck restraint systems and protective equipment. While specific bumper requirements may not be explicitly detailed, general safety standards require employers to provide safe working conditions and protect workers from hazards. Inadequate dock protection systems could result in citations and penalties if they contribute to worker injuries or unsafe conditions.
Industry standards from organizations such as the Dock Equipment Manufacturers Association (DEMA) provide guidance on bumper design, installation, and performance requirements. These standards help ensure compatibility between different manufacturers’ products and establish minimum performance criteria. Following recognized industry standards demonstrates due diligence and helps avoid potential liability issues.
Local building codes may include specific requirements for loading dock construction and safety equipment. These codes vary by jurisdiction and may address bumper specifications, installation methods, or maintenance requirements. Consult local authorities to understand applicable requirements and ensure compliance with all relevant regulations.
Insurance requirements often address loading dock safety and may specify minimum protection standards for coverage eligibility. Some policies require specific equipment or maintenance procedures to maintain coverage. Review your insurance policy requirements and consult with your carrier to understand any bumper-related provisions.
Documentation requirements for safety compliance may include installation records, maintenance logs, and inspection reports. Maintaining comprehensive records demonstrates compliance with safety requirements and provides valuable information for insurance claims or regulatory inquiries. Establish documentation procedures and ensure consistent record-keeping practices.
Conclusion
Selecting the right rubber dock bumper for your truck dock requires careful consideration of multiple factors including facility requirements, environmental conditions, traffic patterns, and budget constraints. The investment in appropriate protection systems pays dividends through reduced maintenance costs, improved safety, and extended equipment life.
Understanding the different types of bumpers available, their performance characteristics, and installation requirements helps ensure your selection meets both immediate needs and long-term expectations. Proper sizing, installation, and maintenance procedures maximize the return on your investment while providing reliable protection for your facility and visiting vehicles.
The cost of adequate protection is minimal compared to the potential expenses of structural damage, equipment failure, or safety incidents resulting from inadequate bumper systems. By following the guidelines and considerations outlined in this guide, you can make an informed decision that provides optimal protection and value for your specific application.
Remember that dock bumper selection is not a one-time decision but an ongoing process that should be reviewed as your facility’s needs change. Regular assessment of performance, wear patterns, and changing requirements ensures your protection system continues to meet your needs effectively and economically.
Certified Material Testing Products (Certified MTP) is a leading supplier of construction materials testing equipment and laboratory supplies in the United States. They offer a comprehensive range of products for testing concrete, asphalt, aggregate, soil, and cement, catering to both field and laboratory applications But no matter whether they are prefered or not, the whole idea behind these tools is similar: getting a polished, shiny, and permanent effect. New to stucco or a seasoned pro, investing in good tools and learning the nuances of their use is what will get you started perfecting your craft.
Frequently Asked Questions (FAQ)
Q: How often should rubber dock bumpers be replaced?
A: Replacement frequency depends on usage patterns, environmental conditions, and bumper quality. High-traffic facilities may require replacement every 2-3 years, while low-usage applications might achieve 5-7 years of service. Regular inspection for signs of wear, compression set, or damage provides the best indication of replacement needs.
Q: Can I install rubber dock bumpers myself, or do I need professional installation?
A: While basic installations can be handled by skilled maintenance personnel, professional installation ensures proper mounting, alignment, and compliance with safety requirements. Complex installations, structural modifications, or specialized applications typically require professional services. Consider your staff’s capabilities and the installation complexity when making this decision.
Q: What’s the difference between laminated and molded rubber dock bumpers?
A: Laminated bumpers consist of multiple rubber layers bonded together, offering good general-purpose protection at reasonable cost. Molded bumpers are created using compression molding techniques, providing superior density consistency and performance characteristics. Molded options typically cost more but offer better durability and performance in demanding applications.
Q: How do I determine the correct size for my dock bumpers?
A: Proper sizing requires measuring your dock configuration and considering the typical vehicles servicing your facility. Width should provide adequate coverage for approach variations, height should match truck bed levels, and thickness should be appropriate for expected impact forces. Consult manufacturer sizing guides and consider professional assessment for complex applications.
Q: Are there special bumpers for extreme weather conditions?
A: Yes, specialty rubber compounds are available for extreme temperature conditions, chemical exposure, and UV resistance. Cold-weather formulations maintain flexibility in sub-freezing temperatures, while UV-resistant compounds prevent premature aging in outdoor installations. These specialty options typically cost more but provide essential protection in challenging environments.
Q: What maintenance is required for rubber dock bumpers?
A: Regular visual inspection for damage, cleaning to remove debris and contaminants, and checking mounting hardware for looseness or corrosion. Establish inspection schedules based on usage patterns and environmental conditions. Document maintenance activities and replace bumpers when wear indicators suggest diminished protection capabilities.
Q: How do I know if my current bumpers need replacement?
A: Signs requiring replacement include visible cracks or tears, compression set where rubber doesn’t return to original shape, chunks missing from the bumper face, loose mounting hardware, or impact damage to surrounding structures. Any condition that compromises impact absorption or protection effectiveness indicates replacement needs.
Q: Can different types of bumpers be mixed on the same dock? A: While possible, mixing different bumper types can create inconsistent protection and appearance issues. Different compression characteristics may result in uneven load distribution and accelerated wear. If mixing is necessary, ensure compatibility and consider the impact on overall system performance.
Q: What’s the typical warranty coverage for rubber dock bumpers?
A: Warranty coverage varies by manufacturer and product type, typically ranging from 1-5 years depending on materials and construction. Coverage usually includes defects in materials and workmanship but may exclude normal wear, impact damage, or environmental degradation. Review warranty terms carefully and understand exclusions before making purchase decisions.
Q: Are there regulations governing dock bumper specifications?
A: While specific bumper regulations may be limited, general safety standards require adequate protection for workers and equipment. OSHA requirements, industry standards, and local building codes may address various aspects of loading dock safety. Consult applicable regulations and consider professional guidance to ensure compliance.